
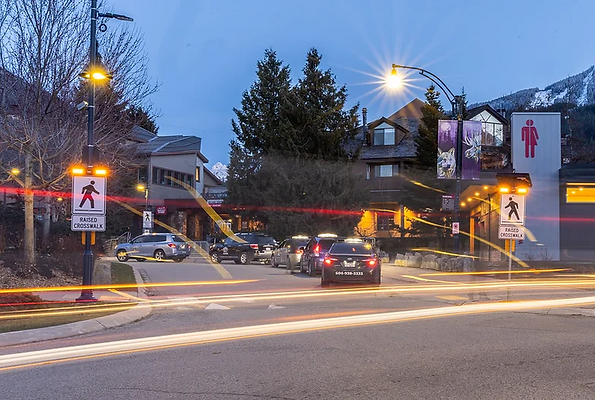
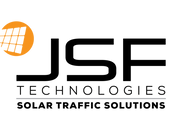
JSF Technologies (JSFT) is a leading manufacturer and supplier within the global transportation industry, specializing in the development and provision of intelligent signaling devices and illumination systems. Traffic solutions need to be robust and durable, lasting for years without maintenance. They are also public facing, and need to be compact, sleek, and aesthetically pleasing.
JSFT was moving towards a large production effort and needed to stay focused on the firmware development of their product. At the same time there was a need to consolidate the SKU’s for the system into a single extensible product and update the mechanical design to prepare for production. To meet tight deadlines and keep their orders on track, JSFT offloaded the mechanical and electrical updates to Motus while they stayed focused on firmware and production.
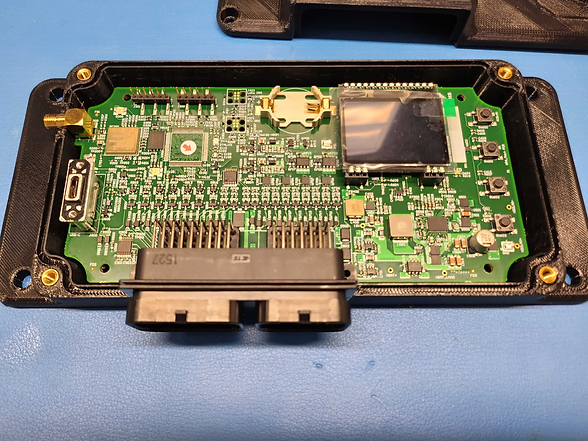
Electrical Design
As JSFT moved to production, minimizing the number of product models and ensuring longevity of design was critical for profitability.
Motus developed a single, extensible board design that consolidated multiple SKUs. This approach:
-
Streamlined JSFT's inventory management process
-
Reduced manufacturing complexity
-
Lowered production costs by minimizing the number of unique components
EMC Support
Motus supported JSFT through the emissions prescan process at QAI Laboratories. Motus provided training and guidance on EMC testing tools, debug techniques, and mitigation strategies. When the JSFT team returned for the complete scan with Motus on deck for remote support, JSFT led the WP6 through successful EMC testing without requiring assistance.

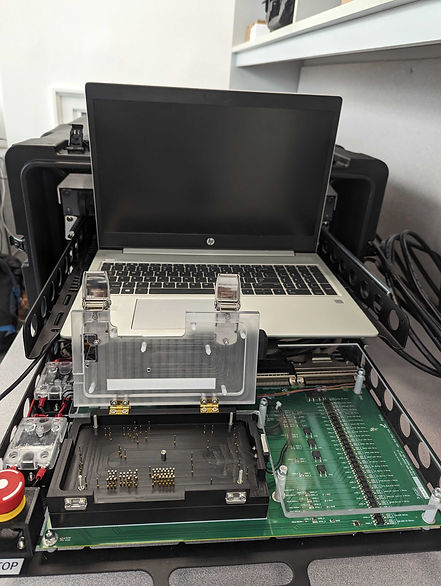
AVS System
As JSFT moved to production, they faced a mounting problem. Their current validation and testing process was time and labor intensive, and prone to error. JSFT needed a solution to dramatically improve validation testing, or else production would fall behind and costs would begin to stack up.
Motus's solution was the Automated Validation System (AVS), a custom-designed testing platform that combined off-the-shelf equipment with bespoke hardware and software. Key features included:
-
Fully automated test procedures
-
Comprehensive test coverage for all possible deployments and configurations
-
Tamper-proof validation reporting
-
Historical tracking of individual units from production to deployment
-
Performance trend analytics
​​
What used to be a tedious manual process that would take hours could now be completed in under 3 minutes.
Results
These projects lead to soaring production, allowing JSFT to meet and exceed delivery timelines. Quality issues were caught earlier, which reduced waste and improved customer satisfaction. JSFT engineers could now accelerate product development since they needed to spend less time troubleshooting.
