

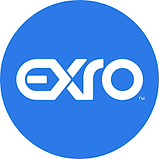
Exro Technologies wanted a scaled up design/prototype of their revolutionary Coil Switching technology for electric vehicles from 500W to 25kW… in three months.
​
Exro approached Motus in early 2020 with an extremely time sensitive power electronics project. Exro had developed a technology called Coil Driver™ that empowers a single motor to act as multiple electric machines, optimizing torque, and power while dynamically maximizing system efficiency. It alters electromagnetics in response to speed and torque changes, reconfiguring coil windings intelligently and seamlessly in both series and parallel modes.
Exro had developed a 500W electric bike proof of concept and came to Motus with a desire to rapidly scale up the technology to a 25kW version suitable for small electric vehicles.
Three Months from Concept to Delivery?
“We’re not sure, but we think we can, and we are definitely willing to try!”
With a three month timeline goal, Motus created a small, focused streamlined team of mechanical, hardware and firmware designers dedicated solely to the Exro project.
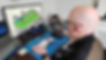

The Design Approach
The integrated electo-mechanical design needed to adhere to UL safety creepage and clearances. Mosfets chosen, heat sink geometry, cooling, airflow, max current, and efficiency targets would all drive each other and the overall form factor. We knew we’d need to rapidly assess and evaluate different design options, so we started by building a full electrical, thermal, and form factor calculation simulation spreadsheet that would rapidly allow us to evaluate the relative performance and tradeoffs of different mosfet, heatsinks, fans, and overall shapes.
It's All in the Details
Once we had the overall architecture figured out, our mechanical, electrical teams designed and fully electrically and thermally simulated the design in less than 5 weeks. All components chosen needed to be available and short lead time (did we mention this was early 2020, right at the onset of Chinese supply chain issues?)
​
25kW meant over 500 amps of current, so large custom copper bus bars needed to be designed and integrated with a novel 6 layer 24oz stitched planes PCBs that housed the mosfets. The stacking and physical arrangement of the boards needed to adhere to all UL creepage and clearance requirements, and flatness in manufacturing and assembly would be crucial to maintain intimate electrical and thermal contact between the copper and the PCBs.
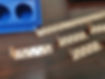
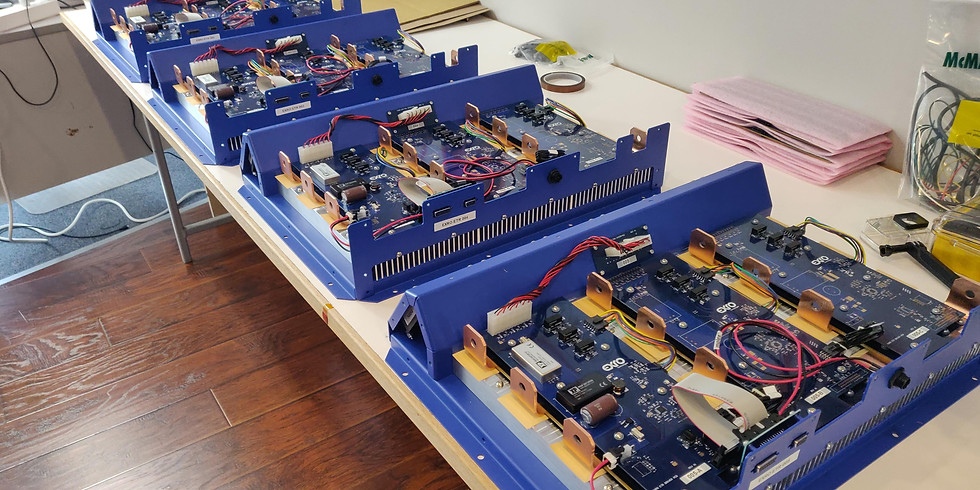

Rapid Prototyping
The next 4 weeks were focused on procurement, vendor support, in house assembly at Motus and testing. Motus implemented a small run QA/QC system and assembly line to build four of the units.
​
Final operational testing was completed on the desk of the Motus CEO, the night before scheduled delivery.