
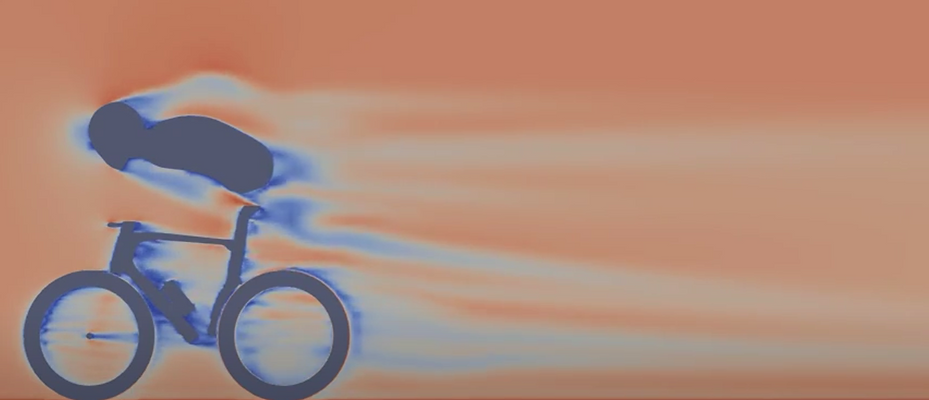
Competitive cycling is highly data-driven, with accurate and accessible sensors widely used to optimize athlete performance. Power meters, speed sensors, and heart rate monitors are common tools cyclists use to support their training. Although a collection of these sensors can provide meaningful information regarding a rider’s physical and physiological states, there is currently no commercial solution to measure and link aerodynamic factors to rider physiology in real-time. There is a trade off between how aerodynamic the rider is (bending towards the handle bars) and how much power they are able to put out. The fastest position is not always the most aerodynamically efficient position.
We set out to develop a full system, called Aerocoach, that would coach users into the optimal position to go the fastest for the least physical effort in real-time under changing road conditions. This optimal position is often counterintuitive, and over time this coaching would teach athletes to ride more efficiently.
Measuring the Wind - Nacelle Unit
The Nacelle’s core function is to measure wind speed as accurately as possible in conditions experienced while cycling. One breakthrough was the inclusion of a multiport design, which enables the sensor to measure airspeed at high degrees of yaw. CFD simulations were used extensively to predict the behavior of various designs in cycling wind conditions. A notable challenge during early prototyping was simulation validation and device calibration. In order to overcome these issues, Motus built their own in-house wind tunnel to validate design choices.


Early Prototyping
The Aerocoach Module needed to be able to reliably measure the profile of the rider's torso while riding in all weather conditions, from bright sun to rain. Recent development in “Time of Flight” sensor technology allowed us to use these light based sensors to get a small array of distance measurements on a rider's torso.
To ensure the depth field measurement would work for cycling we went through a range of tests on a development unit we designed and built. The development unit allowed us to experiment with locations, angles, materials, and lighting conditions to ensure we were getting the best measurements possible.
All of the information gathered went into the design of the final Aerocoach Module. It’s intended to hold a bike computer and the Nacelle while attaching to the handlebars. Three Time of Flight sensors are arranged to capture the full torso and head of any rider up to 6’6” in height.
Testing
The velodrome was chosen as the location for our first outdoor tests. Through testing we were able to accurately evaluate the CdA of a rider for the first time. We were able to see variations in drag due to position changes, and could track the power losses due to drag in real time.
Velodrome testing allowed us to identify several areas for improvement, and demonstrated difficulties we would face when moving to fully uncontrolled outdoor testing. The regular corners revealed the relative velocity differences between the rider's body and the wheels when going through a tight corner. Wind exposure revealed the static pressure variations that occur with differential wind speeds outdoors. Post analysis of results showed variable time delays coming in from the third party wheel speed sensor and power meter.
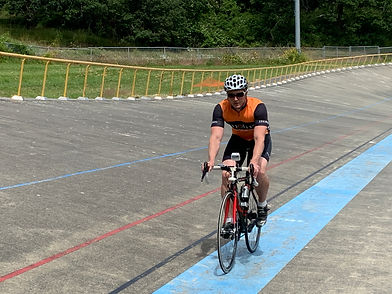

Ready for Industry Partners
The Aerocoach system is a completed, robust preliminary product concept. The combined data from the Nacelle and AC Modules, as well as 3rd party sensors allowed the Motus Design team to create a holistic cycling power model. The Aerocoach system can calculate drag in real time, evaluate and categorize body positions, collect power duration data, and give recommendations to riders based on the live conditions.